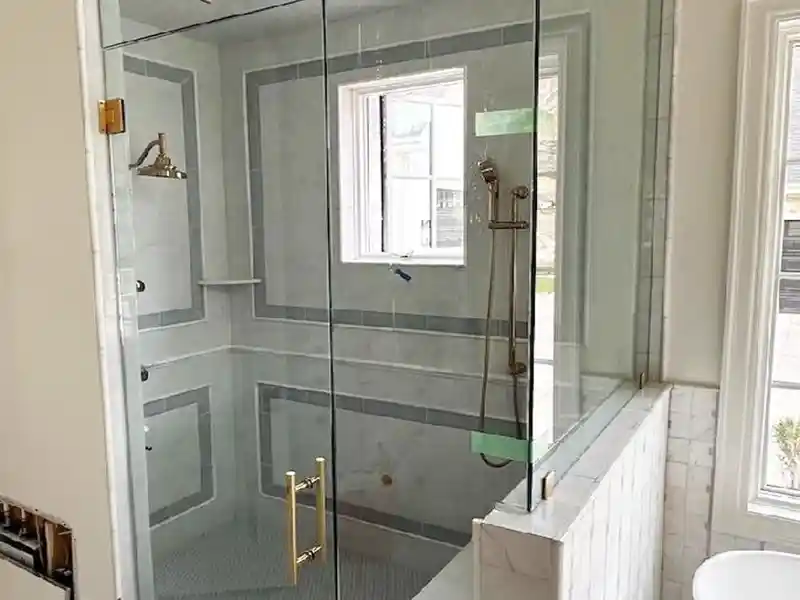
Project description
For multi-level steam showers, it is crucial to accurately measure everything – from the floors, walls and ceilings to every notch and rise. If you measure incorrectly, the glass will not fit perfectly into the existing structure, which will mean more repairs, costs and wasted time.
This is exactly the challenge our colleagues at Jeske Glass faced when creating glass elements for a multi-level steam shower.
- The challenge before Flexijet
Before the Flexijet 3D system, the measurement process typically included: - manual measurement with a tape measure or laser rangefinders,
- using a plumb bob to check verticality,
- additional checks with linear lasers and recording deviations.
Such an approach often brings a high probability of error when transferring measurements to drawings. For projects with multiple levels and a large number of cuts, this could mean multiple trips to the construction site, repeated measurements and unwanted errors when cutting the glass.
- Solution thanks to Flexijet
Unevenness, grooves, protrusions and angles are no longer a problem. All surfaces that need to be precisely measured, with Flexijet will not only be that – all deviations will be taken into account during the design, immediately drawn in the CAD program. This approach has helped our colleagues from Jeske Glass to: - quickly and accurately measure walls, floors, ceilings and other details in the shower cabin,
- automatically transfers measured points to FlexiCAD software, where drawings are available in 2D and 3D views,
- minimizes errors and the need for additional manual measurements, saves time when drafting and cutting glass.
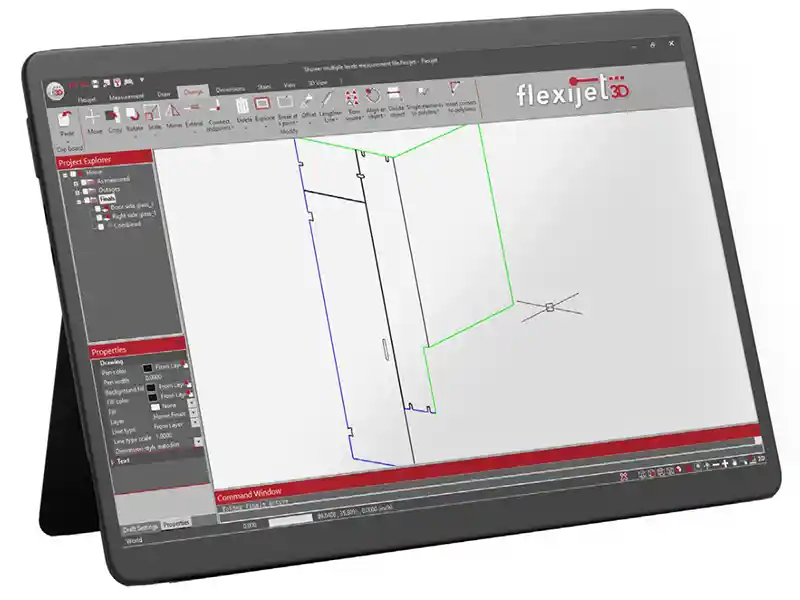
The results and advantages of the Flexijet 3D system are also on this project:
- Reduced the number of glass corrections and finishing.
- Saved working hours and reduced the number of trips to the construction site.
- Improved cooperation with contractors because they are based on precise designs.
- Freed the team from the frustrations that often arise from mismatched dimensions.
According to Jeske Glass owner Rick Jeske, the financial and operational benefits have been significant: “Flexijet is a game changer! I attended GlassBuild 2024 in Dallas and, speaking with other glass business owners, I was told that Flexijet would pay for itself in two years or less, just through labor savings. That’s not even counting fewer repairs, fewer site visits, less crew frustration, and more. We use it for everything!” – Rick Jeske, Jeske Glass
This statement clearly shows that the investment in Flexijet 3D pays off very quickly – not only through savings in labor and materials, but also through greater employee satisfaction and a more professional approach to projects.
Conclusion
In a project to install glass elements for a multi-level steam shower, Jeske Glass used the Flexijet 3D system to achieve perfect fit to every corner, notch and elevation. This avoided unnecessary adjustments and ensured a flawless result.
Flexijet 3D has once again proven itself as a key tool in the modern glass industry – speeding up the process, reducing costs and potential frustration, and improving the final outcome. Thanks to it, our colleagues at Jeske Glass were able to complete the glass fabrication project for this demanding steam shower enclosure with quality, speed, and less stress.