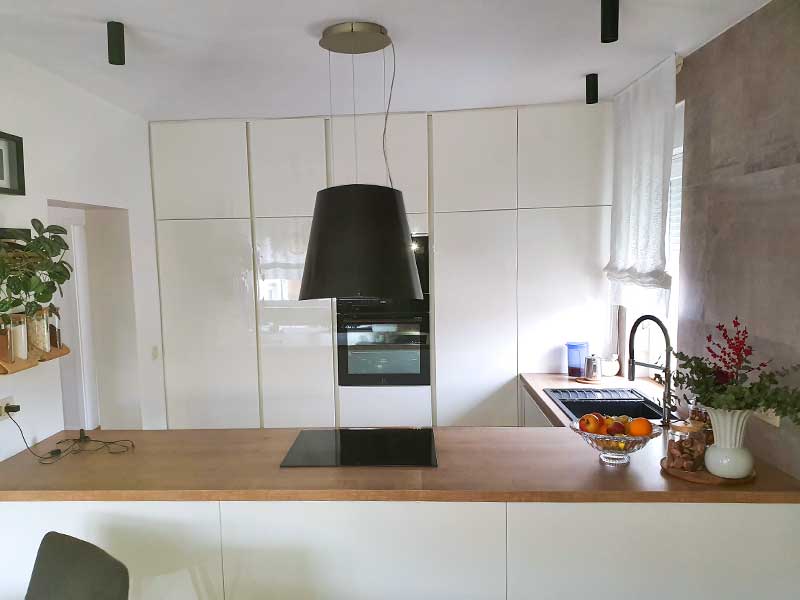
About the project:
In this project the challenge was to fit the countertop perfectly into the space, taking into account all the specificities we encountered, such as the sink, windows, dishwasher, and other elements.
To allow the window to open above the sink, it was necessary to lower the countertop while still maintaining a relatively standard height. The height of the dishwasher and the window sill imposed limitations on us. To overcome these obstacles, we had to thin the countertop by 20 mm on the underside in the area below the window.
After detailed 3D measurements and proper technical preparation, we created CNC files, which the CNC machine used to carry out the rest of the work—precisely shaping the countertop according to our specifications. The installers then had a relatively easy task of placing the countertop in its position and applying a 3 mm silicone seal around it. There was no need for wall trims, as everything fit perfectly as planned.
This project demonstrates that with the right approach and tools, challenges such as window height, sink and dishwasher positions can be turned into opportunities for innovative solutions that combine functionality and style.
Flexijet operator for 3D measurement: Edo Aganović
Project executor: Studio Element d.o.o.
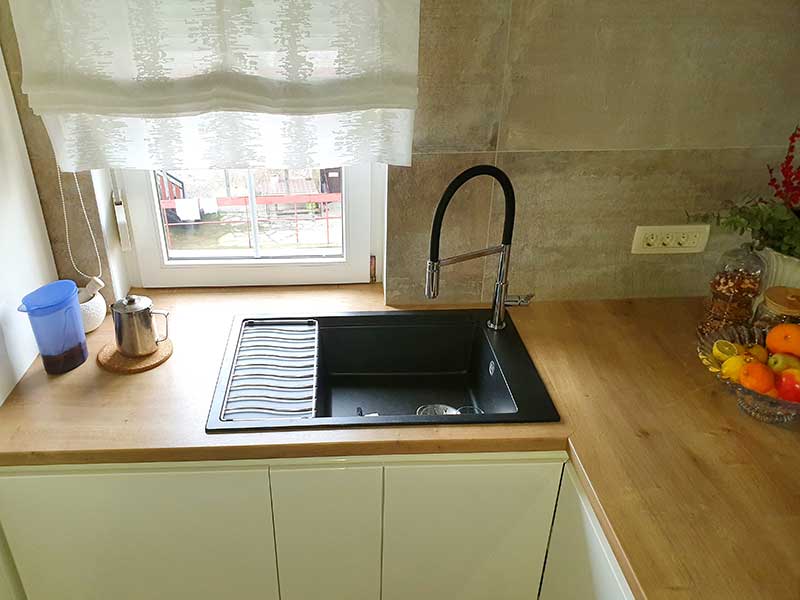
Project summary
The success of this project testifies to the power of digitization in the furniture fabrication process—from initial measurements and technical preparation to fabrication and final installation. It confirms that the proper combination of technology, expertise, and precision is key to the successful realization of even the most complex projects.
- Time required for conventional measurement: impossible to determine
- Time required with Flexijet - 2.5 hours
- Saving time and money: immeasurable
- Efficiency and accuracy: immeasurable